2010/06/27
Problèmes techniques.
Désolé pour le manque de post dernièrement, mais non seulement il ne se passe pas grand chose dans l'actualité, mais en plus mon ordinateur fait des siennes. Il ne semble pas du tout apprécier les chaleurs de l'été. Bref, je ne suis pas capable de faire mes articles comme je le voudrais alors je vais être obligé de prendre une pause d'ici à ce que je me trouve une nouvelle bécane.
2010/06/16
Capsule mécanique - L'allumage 2ième partie.
Je continue aujourd'hui mes capsules mécaniques. Dans mon précédent article, je vous parlais de l'allumage et de sa gestion mécanique. Je vous disais qu'aujourd'hui la plupart des voitures n'utilisent plus ce genre de système et c'est bien vrai. Par contre, les principes de base comme l'avance à l'allumage et le temps d'allumage demeurent les mêmes. C'est seulement la façon dont le tout est géré qui a changé. L'arrivée du transistor et des premiers micro-ordinateurs a changé beaucoup de choses dans la vie de tous les jours et la voiture n'y a pas échappé. Le premier système d'allumage géré électroniquement est apparut en 1955 dans les Formule 1 BRM qui courait à l'époque, tandis que la première voiture de production à être équipée d'un tel système fut une Pontiac de 1963 avec le système Delcotronic.
Aujourd'hui cette méthode est largement répandue et tout moteur qui se respecte en est équipé. C'est pourquoi la deuxième partie de mon article portera sur la gestion électronique de l'allumage.
Ordinateur de contrôle moteur ( « ECU » ou « PCM » en anglais).
On parle de gestion électronique, alors évidemment il y a quelque chose qui va gérer tout ça. Ce quelque chose est carrément un micro-ordinateur. Vous avez peut-être déjà entendu parler d'un ECU ou d'un PCM, ce sont en fait des abréviations pour décrire le dit ordinateur. ECU ça veut dire « Engine Control Unit » en anglais et PCM tient pour « Powetrain Control Module ». Carrément ordinateur de contrôle moteur. C'est le cerveau de votre moteur si vous voulez. On peut le séparer en deux partie. Une partie réceptrice et une partie active. La partie réceptrice recueille différentes informations à partir de plusieurs capteurs situés sur le moteur et sur la transmission. Ces informations sont ensuite envoyées au processeur. Ce dernier analyse l'information et décide d'une stratégie d'action. Cette stratégie est ensuite envoyée aux différents actuateurs contrôlés par le PCM et ces derniers influent directement sur le fonctionnement du moteur. Évidemment, le tout est pré-programmé par les ingénieurs au stade de conception de la voiture. Il est possible de modifier ou hacker ce programme, mais ce sera le sujet d'un futur article.
Dans le cas qui nous intéresse ici, le PCM fera s'allumer et s'éteindre les bougies d'allumage en synchronisme avec les temps moteurs et la charge moteur demandée ( « engine load » en anglais). La charge moteur est tout simplement un idée abstraite qui fait référence au travail qu'on demande au moteur. Littéralement est-ce que notre moteur force ou pas? Ce sont les différents capteurs qui pourront renseigner le PCM sur cette mesure. Je passe en revue ci-dessous les dits capteurs qui ont attrait à l'allumage.
Capteur de position du vilebrequin ( « crankshaft position sensor » en anglais ou abbrègé CPS).
Dans les systèmes les plus rudimentaires, on doit absolument avoir un capteur de position du vilebrequin (CPS). Ce dernier envoi à l'ordinateur la position du vilebrequin et grâce à la programmation, le PCM peut savoir quel piston arrive dans son temps d'allumage et ainsi allumer la bonne bougie à l'aide de la bobine d'allumage.
Le fonctionnement de ce capteur est assez simple. La très grande majorité fonctionne selon le principe de l'effet Hall. Ce principe n'est pas très compliqué et s'apparente un peu au fonctionnement de l'alternateur. On a un bobinage de fil de cuivre qu'on appel relucteur. En faisant passer un aimant permanente devant ce dernier, il se crée un courant électrique grâce au champ magnétique de l'aimant. La variation du courant est le signal qui sera envoyé à l'ECU. Dans la plupart des CPS on a soit une absence de courant ou un courant de 5 volts. C'est donc un signal digital qui sera facilement interprété par le processeur. La petite animation ci-dessous explique très bien en image le fonctionnement.
Les aimants permanents sont le plus souvent situés sur la poulie du vilebrequin à l'extérieur du bloc moteur et le relucteur ou CPS se servira de cette dernière pour déterminer la vitesse de rotation du vilebrequin. Le CPS peut aussi être placé à l'intérieur du bloc, les aimants sont alors intégrés au vilebrequin. On peut aussi placer les aimants sur le volant moteur à l'autre bout du vilebrequin. L'emplacement a peut d'importance en autant que le CPS puisse lire la vitesse du vilebrequin. Certains moteurs utilisent d'autre principe comme un obturateur optique ou un capteur à induction.
Capteur de position de l'arbre à cames ( « camshaft position sensor » ou « cam sensor » en anglais).
Ce capteur sert à déterminer la position de l'arbre à cames. Il n'est pas strictement nécessaire, mais le devient lorsqu'on utilise la distribution variable. La position de l'arbre à cames par rapport à celle du vilebrequin permet de déterminer avec encore plus de précision le moment de l'allumage. La plupart fonctionne d'après l'effet Hall décrit plus haut.
Le capteur est normalement placé dans la culasse près de la poulie d'arbre à cames. Évidemment, si le moteur n'est pas un moteur SACT ou DACT le capteur sera positionné ailleurs en autant qu'il puisse lire facilement la position de l'arbre à cames.
Capteur d'air volumétrique ou barométrique ( « mass airflow meter » ou « manifold air pressure sensor » en anglais ).
Je vous disais plus haut que l'ECU doit aussi déterminer la charge du moteur pour savoir s'il force ou pas. Cette mesure aidera surtout à déterminer, avec l'aide des autres capteurs déjà mentionnés, l'avance à l'allumage. Plus le moteur forcera plus on avancera l'allumage pour que le couple du moteur vienne à bout du travail qu'on lui demande.
Je vous expliquais aussi dans une de mes chroniques précédentes qu'un moteur à explosion est en fait une grosse pompe à air. On doit faire entrer plus d'air pour faire brûler plus d'essence pour avoir plus de puissance. Ça revient donc à dire que plus notre moteur tourne rapidement plus il aspirera d'air par sa tubulure d'admission. Cet air qui est aspiré crée une dépression atmosphérique momentané dans la tubulure d'admission. Cette dépression est appelé « vacuum » en anglais et est très importante. Plus la dépression est forte plus le moteur force. C'est-à-dire que quand le moteur force il tourne moins vite et les pistons ont le temps d'aspiré plus d'air dans la chambre de combustion.
Si on pouvait mesuré cette dépression dans la tubulure d'admission on pourrait mesuré la charge moteur. Eh bien, c'est exactement ce que ces deux capteurs font. Le premier est carrément un baromètre c'est-à-dire qu'il mesure la pression à l'intérieur de la tubulure d'admission, « air intake manifold » en anglais. C'est pourquoi on l'appel « manifold air pressure sensor » ou MAP en abrégé. Il est le plus souvent constitué d'un clapet qui s'ouvrira plus ou moins dépendant du vaccum présent derrière lui. Le degré d'ouverture est alors mesuré par un potentiomètre situé sur la penture du clapet. La variation de voltage de 0 à 5 volts permet au processeur de calculer le vacuum présent dans la tubulure d'admission.
Le capteur d'air volumétrique quant à lui mesure la quantité d'air qui passe dans la tubulure d'admission. Plus l'air passe vite plus la dépression sera faible tandis que plus l'air passe lentement plus elle sera grande. Ce sont les pistons du moteur qui feront accélérer ou ralentir le flux d'air dans la tubulure.
Le capteur utilise normalement un fil métallique où on fait passer un courant électrique. Due à la résistance électrique ce fil s'échauffe. Si on souffle de l'air plus ou moins froid sur ce dernier sa résistance sera plus ou moins grande et il laissera passer plus ou moins d'électricité. Le courant électrique variera ainsi de 0 à 5 volts. C'est ce signal qu'on envoi au processeur et qui lui permettra de déterminer la quantité d'air qui passe dans la tubulure d'admission.
Le gros problème de ces capteurs c'est qu'on doit savoir la température de l'air ambiant pour pouvoir comparer les valeurs mesurés aux tables d'allumage contenu dans le PCM. On doit donc avoir un autre capteur séparé qui mesurera cette température. De plus, idéalement il peut s'avérer utile de connaître la pression atmosphérique ambiante ce sera alors le rôle d'un autre capteur prévu à cet effet.
Bobine d'allumage ( « ignition coil » ou tout simplement « coil » en anglais ).
Dans des moteurs modernes c'est le PCM qui sert de distributeur. Un transistor reçoit le signal du PCM et permet de libérer la charge électrique transformée et accumulée dans la bobine ( Voir la première partie pour plus de détails. ) . Étant donné que le tout est maintenant électronique et non mécanique on peut d'autant plus rapetisser et même miniaturiser la bobine.
Dans le moteur de votre voiture, qui pour les besoins de la cause est équipé d'un moteur 4 cylindres, on a normalement 2 bobines reliés au PCM. C'est ce que l'on appel un système « wasted spak », carrément étincelles perdues. Une bobine contrôle 2 bougies. Le PCM envoi le signal à la bobine et cette dernière décharge son courant dans les bougies auxquelles elle est connecté. Par contre, un seul piston est dans son temps d'explosion, alors l'autre étincelle est gaspillés. Ça n'a pas beaucoup d'importance si ce n'est que la bougie concernée s'allume pour rien. Cela peut amener une usure prématuré, mais ce n'est pas si dramatique. Le plus gros problème c'est que l'avance à l'allumage sera la même pour les deux bougies. Encore là ce n'est pas dramatique, mais dans un monde idéale chaque cylindre doit être contrôlé séparément.
La solution à ce problème est simple, on installe un bobine par bougie. C'est l'allumage direct, « direct ignition » en anglais ou on peut aussi parler de « coil-on-plug ». Coil-on-plug ça veut dire bobine sur bougie. On a donc la bobine qui est directement branché sur la bougie d'allumage et chaque bougie est donc contrôlé directement par le PCM ce qui permet de contrôler avec une extrême précision l'avance à l'allumage et même la tension qui est envoyé dans la bougie. Les moteurs vraiment modernes ou ceux qui ont à cœur notre planète utilisent tous ce système.
C'est tout pour ce soir, étudié bien ça parce que la prochaine étape est l'injection d'essence.
Aujourd'hui cette méthode est largement répandue et tout moteur qui se respecte en est équipé. C'est pourquoi la deuxième partie de mon article portera sur la gestion électronique de l'allumage.
Ordinateur de contrôle moteur ( « ECU » ou « PCM » en anglais).
On parle de gestion électronique, alors évidemment il y a quelque chose qui va gérer tout ça. Ce quelque chose est carrément un micro-ordinateur. Vous avez peut-être déjà entendu parler d'un ECU ou d'un PCM, ce sont en fait des abréviations pour décrire le dit ordinateur. ECU ça veut dire « Engine Control Unit » en anglais et PCM tient pour « Powetrain Control Module ». Carrément ordinateur de contrôle moteur. C'est le cerveau de votre moteur si vous voulez. On peut le séparer en deux partie. Une partie réceptrice et une partie active. La partie réceptrice recueille différentes informations à partir de plusieurs capteurs situés sur le moteur et sur la transmission. Ces informations sont ensuite envoyées au processeur. Ce dernier analyse l'information et décide d'une stratégie d'action. Cette stratégie est ensuite envoyée aux différents actuateurs contrôlés par le PCM et ces derniers influent directement sur le fonctionnement du moteur. Évidemment, le tout est pré-programmé par les ingénieurs au stade de conception de la voiture. Il est possible de modifier ou hacker ce programme, mais ce sera le sujet d'un futur article.
Dans le cas qui nous intéresse ici, le PCM fera s'allumer et s'éteindre les bougies d'allumage en synchronisme avec les temps moteurs et la charge moteur demandée ( « engine load » en anglais). La charge moteur est tout simplement un idée abstraite qui fait référence au travail qu'on demande au moteur. Littéralement est-ce que notre moteur force ou pas? Ce sont les différents capteurs qui pourront renseigner le PCM sur cette mesure. Je passe en revue ci-dessous les dits capteurs qui ont attrait à l'allumage.
Capteur de position du vilebrequin ( « crankshaft position sensor » en anglais ou abbrègé CPS).
Dans les systèmes les plus rudimentaires, on doit absolument avoir un capteur de position du vilebrequin (CPS). Ce dernier envoi à l'ordinateur la position du vilebrequin et grâce à la programmation, le PCM peut savoir quel piston arrive dans son temps d'allumage et ainsi allumer la bonne bougie à l'aide de la bobine d'allumage.
Le fonctionnement de ce capteur est assez simple. La très grande majorité fonctionne selon le principe de l'effet Hall. Ce principe n'est pas très compliqué et s'apparente un peu au fonctionnement de l'alternateur. On a un bobinage de fil de cuivre qu'on appel relucteur. En faisant passer un aimant permanente devant ce dernier, il se crée un courant électrique grâce au champ magnétique de l'aimant. La variation du courant est le signal qui sera envoyé à l'ECU. Dans la plupart des CPS on a soit une absence de courant ou un courant de 5 volts. C'est donc un signal digital qui sera facilement interprété par le processeur. La petite animation ci-dessous explique très bien en image le fonctionnement.
Les aimants permanents sont le plus souvent situés sur la poulie du vilebrequin à l'extérieur du bloc moteur et le relucteur ou CPS se servira de cette dernière pour déterminer la vitesse de rotation du vilebrequin. Le CPS peut aussi être placé à l'intérieur du bloc, les aimants sont alors intégrés au vilebrequin. On peut aussi placer les aimants sur le volant moteur à l'autre bout du vilebrequin. L'emplacement a peut d'importance en autant que le CPS puisse lire la vitesse du vilebrequin. Certains moteurs utilisent d'autre principe comme un obturateur optique ou un capteur à induction.
Capteur de position de l'arbre à cames ( « camshaft position sensor » ou « cam sensor » en anglais).
Ce capteur sert à déterminer la position de l'arbre à cames. Il n'est pas strictement nécessaire, mais le devient lorsqu'on utilise la distribution variable. La position de l'arbre à cames par rapport à celle du vilebrequin permet de déterminer avec encore plus de précision le moment de l'allumage. La plupart fonctionne d'après l'effet Hall décrit plus haut.
Le capteur est normalement placé dans la culasse près de la poulie d'arbre à cames. Évidemment, si le moteur n'est pas un moteur SACT ou DACT le capteur sera positionné ailleurs en autant qu'il puisse lire facilement la position de l'arbre à cames.
Capteur d'air volumétrique ou barométrique ( « mass airflow meter » ou « manifold air pressure sensor » en anglais ).
Je vous disais plus haut que l'ECU doit aussi déterminer la charge du moteur pour savoir s'il force ou pas. Cette mesure aidera surtout à déterminer, avec l'aide des autres capteurs déjà mentionnés, l'avance à l'allumage. Plus le moteur forcera plus on avancera l'allumage pour que le couple du moteur vienne à bout du travail qu'on lui demande.
Je vous expliquais aussi dans une de mes chroniques précédentes qu'un moteur à explosion est en fait une grosse pompe à air. On doit faire entrer plus d'air pour faire brûler plus d'essence pour avoir plus de puissance. Ça revient donc à dire que plus notre moteur tourne rapidement plus il aspirera d'air par sa tubulure d'admission. Cet air qui est aspiré crée une dépression atmosphérique momentané dans la tubulure d'admission. Cette dépression est appelé « vacuum » en anglais et est très importante. Plus la dépression est forte plus le moteur force. C'est-à-dire que quand le moteur force il tourne moins vite et les pistons ont le temps d'aspiré plus d'air dans la chambre de combustion.
Si on pouvait mesuré cette dépression dans la tubulure d'admission on pourrait mesuré la charge moteur. Eh bien, c'est exactement ce que ces deux capteurs font. Le premier est carrément un baromètre c'est-à-dire qu'il mesure la pression à l'intérieur de la tubulure d'admission, « air intake manifold » en anglais. C'est pourquoi on l'appel « manifold air pressure sensor » ou MAP en abrégé. Il est le plus souvent constitué d'un clapet qui s'ouvrira plus ou moins dépendant du vaccum présent derrière lui. Le degré d'ouverture est alors mesuré par un potentiomètre situé sur la penture du clapet. La variation de voltage de 0 à 5 volts permet au processeur de calculer le vacuum présent dans la tubulure d'admission.
Le capteur d'air volumétrique quant à lui mesure la quantité d'air qui passe dans la tubulure d'admission. Plus l'air passe vite plus la dépression sera faible tandis que plus l'air passe lentement plus elle sera grande. Ce sont les pistons du moteur qui feront accélérer ou ralentir le flux d'air dans la tubulure.
Le capteur utilise normalement un fil métallique où on fait passer un courant électrique. Due à la résistance électrique ce fil s'échauffe. Si on souffle de l'air plus ou moins froid sur ce dernier sa résistance sera plus ou moins grande et il laissera passer plus ou moins d'électricité. Le courant électrique variera ainsi de 0 à 5 volts. C'est ce signal qu'on envoi au processeur et qui lui permettra de déterminer la quantité d'air qui passe dans la tubulure d'admission.
Le gros problème de ces capteurs c'est qu'on doit savoir la température de l'air ambiant pour pouvoir comparer les valeurs mesurés aux tables d'allumage contenu dans le PCM. On doit donc avoir un autre capteur séparé qui mesurera cette température. De plus, idéalement il peut s'avérer utile de connaître la pression atmosphérique ambiante ce sera alors le rôle d'un autre capteur prévu à cet effet.
Bobine d'allumage ( « ignition coil » ou tout simplement « coil » en anglais ).
Dans des moteurs modernes c'est le PCM qui sert de distributeur. Un transistor reçoit le signal du PCM et permet de libérer la charge électrique transformée et accumulée dans la bobine ( Voir la première partie pour plus de détails. ) . Étant donné que le tout est maintenant électronique et non mécanique on peut d'autant plus rapetisser et même miniaturiser la bobine.
Dans le moteur de votre voiture, qui pour les besoins de la cause est équipé d'un moteur 4 cylindres, on a normalement 2 bobines reliés au PCM. C'est ce que l'on appel un système « wasted spak », carrément étincelles perdues. Une bobine contrôle 2 bougies. Le PCM envoi le signal à la bobine et cette dernière décharge son courant dans les bougies auxquelles elle est connecté. Par contre, un seul piston est dans son temps d'explosion, alors l'autre étincelle est gaspillés. Ça n'a pas beaucoup d'importance si ce n'est que la bougie concernée s'allume pour rien. Cela peut amener une usure prématuré, mais ce n'est pas si dramatique. Le plus gros problème c'est que l'avance à l'allumage sera la même pour les deux bougies. Encore là ce n'est pas dramatique, mais dans un monde idéale chaque cylindre doit être contrôlé séparément.
La solution à ce problème est simple, on installe un bobine par bougie. C'est l'allumage direct, « direct ignition » en anglais ou on peut aussi parler de « coil-on-plug ». Coil-on-plug ça veut dire bobine sur bougie. On a donc la bobine qui est directement branché sur la bougie d'allumage et chaque bougie est donc contrôlé directement par le PCM ce qui permet de contrôler avec une extrême précision l'avance à l'allumage et même la tension qui est envoyé dans la bougie. Les moteurs vraiment modernes ou ceux qui ont à cœur notre planète utilisent tous ce système.
C'est tout pour ce soir, étudié bien ça parce que la prochaine étape est l'injection d'essence.
2010/06/05
Nissan et le gouvernment québecois signent une entente.
Nissan Canada s'entend avec le gouvernement du Québec pour fournir des points de recharge.
Le premier scoop du Blog Automobile de Phil, enfin je crois. Semblerait que Nissan Canada , le Ministère des ressources naturelles, Hydro-Québec, la ville de Québec et la ville de Montréal est signé une entente dans le but de fournir des points de recharge dans les deux villes concernés. Ces points permettraient au véhicule tout électrique Nissan LEAF de pouvoir circuler dans les dites villes. La Nissan LEAF est présentement en production et a déjà commencée à être vendue dans certaines villes japonaises, européennes et américaines. Pour l'instant, elle n'est pas disponible au Québec, mais elle devrait entrer dans nos concessionnaires d'ici la fin de 2011.
La Nissan LEAF n'est pas une hybride, mais bien une voiture tout électrique. C'est une petite familiale compacte ayant 5 places et 5 portes (hatchback). Elle utilise des batteries lithium-ion semblables aux batteries de téléphones ou d'ordinateurs portables. Semblerait qu'avec une pleine charge elle peut parcourir 160 km en ville et à des vitesses correspondantes. La vitesse maximum est de 140 km/h et le moteur développe 110 Hp et 210 lb-ft. Avec le fil fournit avec la voiture la LEAF se recharge complètement en 20 heures à partir d'une connexion de maison, soit 110 volts à 20 ampères. Évidemment, si on peut la brancher sur du 220 volts le temps de recharge baisse de beaucoup, environ 8 heures. Ça devient acceptable surtout si on fait ça pendant la nuit où normalement on a pas besoin de sa voiture. On peut recharger la LEAF à 80 % en 30 minutes en utilisant un kit de rechargement de 500 volts vendues par Nissan. Le kit coûte environ 16 000$ US. Par contre, il est plus destinés aux concessions ou comme dans l'entente décrite ci-haut à des points de recharge fournit par les villes ou gouvernement.
Dans la même veine, le plan de partage d'auto Communauto a annoncé qu'elle entendait acheter 50 Nissan LEAF pour l'offrir à ces quelques 20 000 usagers. Hydro-Québec, grâce à l'entente signée avec Nissan Canada s'occupera de fournir les points de recharge aux différentes base d'opération de Communauto. La LEAF devrait être disponible à Québec et Montréal.
Personnellement, je trouve que c'est un pas dans la bonne direction surtout pour le transport urbain. Avec 160 km d'autonomie c'est amplement suffisant pour faire vos commissions ou aller travailler au centre-ville. Par contre, oublier vos vacances en Gaspésie on a tout simplement pas assez d'autonomie et les points de recharge seront probablement concentrés dans les grandes agglomérations. CAA viendra pas vous dépanner dans le Parc si ça prend 20 heures recharger votre voiture. En attendant, je vous laisse admirer la voiture, quoiqu'elle n'a pas une beauté.
Commercial de la Lexus LF-A.
Dans un tout ordre d'idée et je dois l'avouer un but un peu moins écolos. Lexus nous dévoile un commercial télé qui est diffusé sur les chaînes câblés américaines. On y voit la LF-A brisé un verre de champagne simplement grâce au son de son échappement. Il n'y aucun trucage, seule le type de verre a été choisis par des experts pour être sur que ça fonctionnerait. C'est tout de même très impressionnant et quel son magnifique. Voici le dit vidéo.
La Lexus LF-A est une voiture hypersports. Elle a un V10 de 4,8 L dérivé de la Formule 1. Le moteur développe 560 Hp à 8 700 tr/min. et 354 lb-ft à 6 800 tr/min. et le rupteur s'engage à 9 500 tr/min. Le tout propulse le magnifique coupé à 326 km/h. La LF-A fait le 0-100 km/h en 3,6 secondes, le 0-200 km/h en 12,9 secondes. Ses freins en carbone lui permette de s'arrêter complètement à partir de 110 km/h en 48 mètres ( 156 pieds ). Le tout est à vous pour la modique somme de 375 000$US si vous pouvez en trouver une, puisqu'elle sont toutes vendues. Voici une galerie de photos pour vous contenter.
Le premier scoop du Blog Automobile de Phil, enfin je crois. Semblerait que Nissan Canada , le Ministère des ressources naturelles, Hydro-Québec, la ville de Québec et la ville de Montréal est signé une entente dans le but de fournir des points de recharge dans les deux villes concernés. Ces points permettraient au véhicule tout électrique Nissan LEAF de pouvoir circuler dans les dites villes. La Nissan LEAF est présentement en production et a déjà commencée à être vendue dans certaines villes japonaises, européennes et américaines. Pour l'instant, elle n'est pas disponible au Québec, mais elle devrait entrer dans nos concessionnaires d'ici la fin de 2011.
La Nissan LEAF n'est pas une hybride, mais bien une voiture tout électrique. C'est une petite familiale compacte ayant 5 places et 5 portes (hatchback). Elle utilise des batteries lithium-ion semblables aux batteries de téléphones ou d'ordinateurs portables. Semblerait qu'avec une pleine charge elle peut parcourir 160 km en ville et à des vitesses correspondantes. La vitesse maximum est de 140 km/h et le moteur développe 110 Hp et 210 lb-ft. Avec le fil fournit avec la voiture la LEAF se recharge complètement en 20 heures à partir d'une connexion de maison, soit 110 volts à 20 ampères. Évidemment, si on peut la brancher sur du 220 volts le temps de recharge baisse de beaucoup, environ 8 heures. Ça devient acceptable surtout si on fait ça pendant la nuit où normalement on a pas besoin de sa voiture. On peut recharger la LEAF à 80 % en 30 minutes en utilisant un kit de rechargement de 500 volts vendues par Nissan. Le kit coûte environ 16 000$ US. Par contre, il est plus destinés aux concessions ou comme dans l'entente décrite ci-haut à des points de recharge fournit par les villes ou gouvernement.
Dans la même veine, le plan de partage d'auto Communauto a annoncé qu'elle entendait acheter 50 Nissan LEAF pour l'offrir à ces quelques 20 000 usagers. Hydro-Québec, grâce à l'entente signée avec Nissan Canada s'occupera de fournir les points de recharge aux différentes base d'opération de Communauto. La LEAF devrait être disponible à Québec et Montréal.
Personnellement, je trouve que c'est un pas dans la bonne direction surtout pour le transport urbain. Avec 160 km d'autonomie c'est amplement suffisant pour faire vos commissions ou aller travailler au centre-ville. Par contre, oublier vos vacances en Gaspésie on a tout simplement pas assez d'autonomie et les points de recharge seront probablement concentrés dans les grandes agglomérations. CAA viendra pas vous dépanner dans le Parc si ça prend 20 heures recharger votre voiture. En attendant, je vous laisse admirer la voiture, quoiqu'elle n'a pas une beauté.
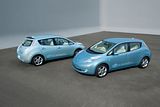
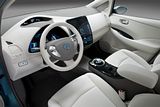
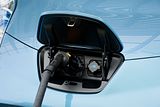
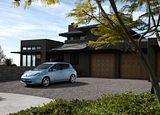
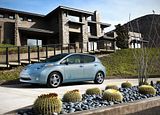
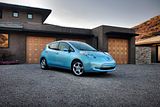
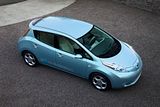
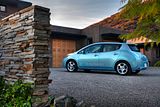
Commercial de la Lexus LF-A.
Dans un tout ordre d'idée et je dois l'avouer un but un peu moins écolos. Lexus nous dévoile un commercial télé qui est diffusé sur les chaînes câblés américaines. On y voit la LF-A brisé un verre de champagne simplement grâce au son de son échappement. Il n'y aucun trucage, seule le type de verre a été choisis par des experts pour être sur que ça fonctionnerait. C'est tout de même très impressionnant et quel son magnifique. Voici le dit vidéo.
La Lexus LF-A est une voiture hypersports. Elle a un V10 de 4,8 L dérivé de la Formule 1. Le moteur développe 560 Hp à 8 700 tr/min. et 354 lb-ft à 6 800 tr/min. et le rupteur s'engage à 9 500 tr/min. Le tout propulse le magnifique coupé à 326 km/h. La LF-A fait le 0-100 km/h en 3,6 secondes, le 0-200 km/h en 12,9 secondes. Ses freins en carbone lui permette de s'arrêter complètement à partir de 110 km/h en 48 mètres ( 156 pieds ). Le tout est à vous pour la modique somme de 375 000$US si vous pouvez en trouver une, puisqu'elle sont toutes vendues. Voici une galerie de photos pour vous contenter.
2010/06/03
Capsule mécanique - L'allumage.
Bon encore une fois il ne se passe pas grande chose dans le monde automobile. Ce fut un mois de mai plutôt plate et j'espère que le mois de juin ne sera pas du même goût. J'en profite donc pour continuer mes petites capsules mécaniques.
Petit récapitulatif; jusqu'à maintenant on a vu les temps moteurs, les composantes moteurs et la distribution. Dans la dernière leçon je vous parlais du rapport stœchiométrique et du triangle du feu. Je vais revenir sur ce dernier ici. Comme je le disais pour avoir du feu on a besoin de trois choses, un carburant (l'essence), un comburant (l'oxygène dans l'air) et de la chaleur. Jusqu'à maintenant, je vous ai expliqué comment les deux premiers pouvaient entrer dans la chambre de combustion. C'est bien beau tout cela, mais où on prend notre chaleur? Déjà le fait de compresser notre mélange air-essence à l'aide du piston en crée beaucoup, mais ce n'est pas suffisant. C'est ici qu'entre en jeu la fameuse bougie et on nomme les systèmes qui la gère, l'allumage. C'est donc de l'allumage que je vais vous jaser aujourd'hui. On va y aller en ordre décroissant en partant de la chambre de combustion et en sortant du bloc moteur.
La bougie d'allumage (« spark plug » en anglais).
Comme je le disais plus haut, c'est la bougie qui amène la chaleur dans notre triangle du feu. Il s'agit en fait d'un petit dispositif électrique qui émet une étincelle au moment voulut. Cette étincelle allumera à son tour le mélange air-essence. C'est pas vraiment plus compliqué que ça en théorie, mais en pratique il y a beaucoup de petits détails.
Premièrement, on a au minimum une bougie par cylindres. Donc, dans un moteur quatre cylindres on aura quatre bougies. Des moteurs plus archaïques ou demandant plus de chaleur peuvent utiliser plus d'une bougie, mais c'est plutôt l'exception que la règle. On peut facilement savoir à quel type de moteur on a affaire en comptant le nombre de fils à bougie que l'on voit sous le capot. Un moteur 4 cylindres par exemple aura 4 fils à bougies.
Regardez bien la photo ci-dessous je vous l'explique en détails.
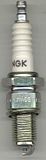
La bougie est normalement placée, dans cette position, dans un orifice prévu à cet effet dans la culasse du moteur. Les filets métalliques que l'on voit dans le bas viennent se visser dans les filets correspondants sur la culasse. Tout de suite au-dessus de ça, on a un bout de métal hexagonal qui vous permettra, avec une douille hexagonale de la même dimension, de dévisser la bougie. La partie blanche est normalement fait en céramique, quoique d'autres matériaux ont été ou sont utilisés. Elle isole le corps de la bougie du courant électrique qui traversera l'électrode. Tout en haut, c'est là que le fil à bougie viendra se connecter pour amener l'électricité. J'oubliais le plus important, l'espèce de petit crochet tout en bas est l'électrode. C'est elle qui produira l'étincelle tant recherché.
On va se concentrer sur l'électrode pour l'instant. On envoi un haut voltage dans la cathode, la partie qui est tout en bas sur la photo juste en-haut du petit crochet. Quand le courant arrive à cet endroit il n'y a plus de conducteur où les électrons peuvent se déplacer. Étant donné qu'un courant électrique cherche toujours à retourner à la terre de la façon la plus « facile » possible, le seul endroit où cela devient possible est l'anode. L'anode c'est le petit crochet justement. Vous remarquerez qu'il ne touche pas du tout à la cathode. Pourtant due au haut voltage de la cathode, le courant passera quand même. Il se créera alors un arc électrique. Cet arc électrique c'est notre étincelle. En fait, l'air ambiant ou dans notre cas le mélange air-essence, s'ionisera et deviendra conducteur, un peu à la façon d'un éclair lors d'un orage. C'est exactement le même principe. Il est alors facile de comprendre que le mélange air-essence, ainsi ionisé, devient extrêmement chaud. Un éclair peut facilement enflammer un arbre comme le prouve chaque été nos nombreux feux de forêt. Ce petit volume de mélange air-essence ionisé créera assez de chaleur pour allumer le reste du mélange. Et voilà, on a notre chaleur dans le triangle du feu et notre explosion dans le moteur.
Évidemment, on a besoin de beaucoup d'électricité pour accomplir cette tâche. Si on compare un courant électrique à un tuyau d'eau, on besoin de beaucoup de pression pour que l'électricité est assez d'énergie pour passer de la cathode à l'anode. Cette « pression », c'est ce que l'on appelle le voltage et on la mesure en volts. Pour que la bougie s'allume convenablement on a besoin de 10 000 à 20 000 volts dépendent de la bougie et de la construction du moteur. De plus, l'espace entre la cathode et l'anode est extrêmement important. Si l'espace est trop petit, l'arc électrique sera faible et ne sera pas suffisant pour enflammer le mélange. Si l'espace est trop grand, on aura peut-être pas assez de voltage pour créer l'arc tant convoité. Ces deux critères sont normalement décidés au moment du design du moteur. C'est pourquoi chaque modèle moteur nécessite des bougies spécifiques. On ne peut pas mettre des bougies d'un moteur Honda dans un moteur de Volkswagen etc...
L'espace entre la cathode et l'anode est ce que l'on appel le « gap » en anglais. Ça veut dire carrément trou ou espace. Si on veut on peut jouer avec cet espace pour avoir plus ou moins de performance. Je ne rentrerai pas dans les détails tout de suite, laissez plutôt ça à votre mécanicien d'expérience.
Le distributeur (« distributor » en anglais).
Pour ceux qui ont compris mes précédentes capsules il vous est évident que les bougies ne s'allument pas tous au même moment. En fait, théoriquement chaque bougie s'allumera seulement au moment où le piston qui lui est assigné entrera dans son temps d'explosion. Ce ne fut pas toujours le cas, mais je reviendrai sur ça plus bas. Pour synchroniser bougies et pistons on a crée ce que l'on appelle le distributeur. Il s'agit la plupart du temps d'un dispositif purement mécanique.
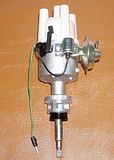
Sur la photo ci-dessus on voit un bel exemple d'un distributeur. La longue partie en métal vient normalement se connecter à ou aux arbres à cames quoique certain distributeur utilise le vilebrequin. Cet arbre tournera à la même vitesse que l'arbre à cames et c'est lui qui envoi le « signal » d'allumage au chapeau de distribution (« distributor cap » en anglais). C'est ce dernier qui nous intéresse ici.
Dans le chapeau, on a un rotor qui est branché sur l'arbre à cames. Il tourne à la même vitesse que ce dernier et distribuera le courant électrique sur les pointes qui sont reliés aux fils à bougies qui amèneront le courant à ces dernières. Le courant arrive de la bobine d'allumage par le centre du chapeau. C'est pas vraiment plus compliqué que ça. Les pointes sont placées précisément pour envoyer le courant électrique au bon moment au cylindre concerné.
Évidemment, les distributeurs peuvent être un peu plus compliqués. On peut se servir du vide créé par un moteur qui force pour faire avancer ou reculer le temps d'allumage des bougies. Le rotor est alors articulé en conséquence et les pointes se déplacent. Pourquoi voudrait-on faire cela? C'est une très bonne question et je vais tenter d'y répondre simplement.
Bon, rappelez vous vos temps moteurs. Le piston remonte vers le point mort haut pour compresser le mélange air-essence. La bougie s'allume ensuite et enflamme le mélange air-essence ce qui pousse le piston vers le point mort bas. C'est bien beau tout ça, mais le mélange air-essence prend du temps à brûler, c'est pas visible à l'œil nu, mais néanmoins vrai. À 6000 tr/min., dans un moteur 4 cylindres, la bougie s'allumera 750 fois par minute dans chaque cylindre. C'est-à-dire que théoriquement le mélange air-essence doit se consumer complètement en 8 centièmes de secondes. C'est trop rapide, l'essence n'aura pas le temps de brûler au complet et on perdra de la puissance. C'est pourquoi on allumera la bougie avant que le piston se retrouve au point mort haut entre son temps de compression et d'explosion. Le mélange air-essence aura eu le temps de brûler un peu et la pression sera à son maximum lorsque ce sera le temps pour le piston de redescendre. On mesure le temps où la bougie s'allume en degré de rotation du vilebrequin. On dira ainsi que la plupart des moteurs ont une avance d'allumage de 20 degrés avant le point mort haut. On y va dans la langue de Shakespeare; « 20 degrees before top dead centre » ou en abrégé 20 deg. BTDC. C'est en général et c'est quelque-chose qui est normalement réglé par le constructeur. Par contre, des ajustements sont possibles et c'est là que votre mécanicien expérimenté entre en jeu. Ce serait trop long de vous expliquez ici tous les détails suffit de dire qu'en règle général si on avance trop l'allumage, disons 25 degrés BTDC, le mélange air-essence s'allumera alors que le piston est encore en train de remonter et on aura détonation (moteur scrappe) et une perte de puissance. Dans le cas contraire, disons 15 degrés BTDC, le mélange air-essence s'allumera quand le piston est en train de redescendre et la pression diminuera d'autant. Résultat, perte de puissance, essence non brûlés et émissions de polluants accrus. Bon maintenant, qu'on a compris ça oubliez tout ce que je viens de vous dire puisque les distributeurs ne sont plus utilisés depuis une bonne dizaine d'années. (Pas vrai essayez de vous en rappeler quand même un peu.)
La ou les bobines d'allumage (« ignition coil » en anglais ou simplement « coil »).
Au début je vous disais que les bougies nécessitent un voltage de 10 000 à 20 000 volts pour bien fonctionner. Évidemment, la batterie fournit seulement 12 volts, on doit donc trouver un moyen de faire augmenter le voltage. C'est le rôle de la bobine d'allumage. Elle fonctionne un peu comme un transformateur électrique accroché à un poteau de téléphone. On a des bobinages de fil de cuivre enroulés autour d'un fil qui part de la batterie. Ces bobinages, par induction électromagnétique, font augmenter le voltage qui est ensuite envoyé vers le distributeur. Et voilà on est passé de 12 à 10 000 volts. En réalité c'est un peu plus compliqué, mais c'est pas un cours d'électricien que je vous fais. Ce que vous devez savoir c'est que si jamais la bobine n'augmente pas le voltage suffisamment, les bougies n'allumeront pas et le moteur ne fonctionnera pas.
En conclusion je vous présent le petit schéma suivant.
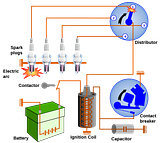
On a la batterie en vert qui fournit le courant à la bobine en gris foncé. Cette dernière augmente le voltage et envoi le courant dans le distributeur, les deux cercles en bleu. Ce dernier s'assure que chaque bougie, les quatre « bâtons » blancs, s'allument au moment désiré. Et voilà, le système d'allumage décrit en une seule image. Le petit truc écrit « capacitor » en anglais, est un accumulateur, ils s'assurent que toutes les interférences électriques qui pourrait être créés n'affectent pas les autres systèmes électriques de votre voiture. En clair, il est là pour ne pas que vous entendiez le distributeur au lieu de CHOI Radio X.
C'est tout pour ce soir, apprenez ça par cœur et je vous reviens avec la version électronique de tout ce bazar. Oh!, j'oubliais. Si vous avez des questions, gênez-vous pas pour vous servir de l'option « commentaires » du blog.
Petit récapitulatif; jusqu'à maintenant on a vu les temps moteurs, les composantes moteurs et la distribution. Dans la dernière leçon je vous parlais du rapport stœchiométrique et du triangle du feu. Je vais revenir sur ce dernier ici. Comme je le disais pour avoir du feu on a besoin de trois choses, un carburant (l'essence), un comburant (l'oxygène dans l'air) et de la chaleur. Jusqu'à maintenant, je vous ai expliqué comment les deux premiers pouvaient entrer dans la chambre de combustion. C'est bien beau tout cela, mais où on prend notre chaleur? Déjà le fait de compresser notre mélange air-essence à l'aide du piston en crée beaucoup, mais ce n'est pas suffisant. C'est ici qu'entre en jeu la fameuse bougie et on nomme les systèmes qui la gère, l'allumage. C'est donc de l'allumage que je vais vous jaser aujourd'hui. On va y aller en ordre décroissant en partant de la chambre de combustion et en sortant du bloc moteur.
La bougie d'allumage (« spark plug » en anglais).
Comme je le disais plus haut, c'est la bougie qui amène la chaleur dans notre triangle du feu. Il s'agit en fait d'un petit dispositif électrique qui émet une étincelle au moment voulut. Cette étincelle allumera à son tour le mélange air-essence. C'est pas vraiment plus compliqué que ça en théorie, mais en pratique il y a beaucoup de petits détails.
Premièrement, on a au minimum une bougie par cylindres. Donc, dans un moteur quatre cylindres on aura quatre bougies. Des moteurs plus archaïques ou demandant plus de chaleur peuvent utiliser plus d'une bougie, mais c'est plutôt l'exception que la règle. On peut facilement savoir à quel type de moteur on a affaire en comptant le nombre de fils à bougie que l'on voit sous le capot. Un moteur 4 cylindres par exemple aura 4 fils à bougies.
Regardez bien la photo ci-dessous je vous l'explique en détails.
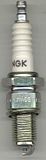
La bougie est normalement placée, dans cette position, dans un orifice prévu à cet effet dans la culasse du moteur. Les filets métalliques que l'on voit dans le bas viennent se visser dans les filets correspondants sur la culasse. Tout de suite au-dessus de ça, on a un bout de métal hexagonal qui vous permettra, avec une douille hexagonale de la même dimension, de dévisser la bougie. La partie blanche est normalement fait en céramique, quoique d'autres matériaux ont été ou sont utilisés. Elle isole le corps de la bougie du courant électrique qui traversera l'électrode. Tout en haut, c'est là que le fil à bougie viendra se connecter pour amener l'électricité. J'oubliais le plus important, l'espèce de petit crochet tout en bas est l'électrode. C'est elle qui produira l'étincelle tant recherché.
On va se concentrer sur l'électrode pour l'instant. On envoi un haut voltage dans la cathode, la partie qui est tout en bas sur la photo juste en-haut du petit crochet. Quand le courant arrive à cet endroit il n'y a plus de conducteur où les électrons peuvent se déplacer. Étant donné qu'un courant électrique cherche toujours à retourner à la terre de la façon la plus « facile » possible, le seul endroit où cela devient possible est l'anode. L'anode c'est le petit crochet justement. Vous remarquerez qu'il ne touche pas du tout à la cathode. Pourtant due au haut voltage de la cathode, le courant passera quand même. Il se créera alors un arc électrique. Cet arc électrique c'est notre étincelle. En fait, l'air ambiant ou dans notre cas le mélange air-essence, s'ionisera et deviendra conducteur, un peu à la façon d'un éclair lors d'un orage. C'est exactement le même principe. Il est alors facile de comprendre que le mélange air-essence, ainsi ionisé, devient extrêmement chaud. Un éclair peut facilement enflammer un arbre comme le prouve chaque été nos nombreux feux de forêt. Ce petit volume de mélange air-essence ionisé créera assez de chaleur pour allumer le reste du mélange. Et voilà, on a notre chaleur dans le triangle du feu et notre explosion dans le moteur.
Évidemment, on a besoin de beaucoup d'électricité pour accomplir cette tâche. Si on compare un courant électrique à un tuyau d'eau, on besoin de beaucoup de pression pour que l'électricité est assez d'énergie pour passer de la cathode à l'anode. Cette « pression », c'est ce que l'on appelle le voltage et on la mesure en volts. Pour que la bougie s'allume convenablement on a besoin de 10 000 à 20 000 volts dépendent de la bougie et de la construction du moteur. De plus, l'espace entre la cathode et l'anode est extrêmement important. Si l'espace est trop petit, l'arc électrique sera faible et ne sera pas suffisant pour enflammer le mélange. Si l'espace est trop grand, on aura peut-être pas assez de voltage pour créer l'arc tant convoité. Ces deux critères sont normalement décidés au moment du design du moteur. C'est pourquoi chaque modèle moteur nécessite des bougies spécifiques. On ne peut pas mettre des bougies d'un moteur Honda dans un moteur de Volkswagen etc...
L'espace entre la cathode et l'anode est ce que l'on appel le « gap » en anglais. Ça veut dire carrément trou ou espace. Si on veut on peut jouer avec cet espace pour avoir plus ou moins de performance. Je ne rentrerai pas dans les détails tout de suite, laissez plutôt ça à votre mécanicien d'expérience.
Le distributeur (« distributor » en anglais).
Pour ceux qui ont compris mes précédentes capsules il vous est évident que les bougies ne s'allument pas tous au même moment. En fait, théoriquement chaque bougie s'allumera seulement au moment où le piston qui lui est assigné entrera dans son temps d'explosion. Ce ne fut pas toujours le cas, mais je reviendrai sur ça plus bas. Pour synchroniser bougies et pistons on a crée ce que l'on appelle le distributeur. Il s'agit la plupart du temps d'un dispositif purement mécanique.
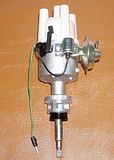
Sur la photo ci-dessus on voit un bel exemple d'un distributeur. La longue partie en métal vient normalement se connecter à ou aux arbres à cames quoique certain distributeur utilise le vilebrequin. Cet arbre tournera à la même vitesse que l'arbre à cames et c'est lui qui envoi le « signal » d'allumage au chapeau de distribution (« distributor cap » en anglais). C'est ce dernier qui nous intéresse ici.
Dans le chapeau, on a un rotor qui est branché sur l'arbre à cames. Il tourne à la même vitesse que ce dernier et distribuera le courant électrique sur les pointes qui sont reliés aux fils à bougies qui amèneront le courant à ces dernières. Le courant arrive de la bobine d'allumage par le centre du chapeau. C'est pas vraiment plus compliqué que ça. Les pointes sont placées précisément pour envoyer le courant électrique au bon moment au cylindre concerné.
Évidemment, les distributeurs peuvent être un peu plus compliqués. On peut se servir du vide créé par un moteur qui force pour faire avancer ou reculer le temps d'allumage des bougies. Le rotor est alors articulé en conséquence et les pointes se déplacent. Pourquoi voudrait-on faire cela? C'est une très bonne question et je vais tenter d'y répondre simplement.
Bon, rappelez vous vos temps moteurs. Le piston remonte vers le point mort haut pour compresser le mélange air-essence. La bougie s'allume ensuite et enflamme le mélange air-essence ce qui pousse le piston vers le point mort bas. C'est bien beau tout ça, mais le mélange air-essence prend du temps à brûler, c'est pas visible à l'œil nu, mais néanmoins vrai. À 6000 tr/min., dans un moteur 4 cylindres, la bougie s'allumera 750 fois par minute dans chaque cylindre. C'est-à-dire que théoriquement le mélange air-essence doit se consumer complètement en 8 centièmes de secondes. C'est trop rapide, l'essence n'aura pas le temps de brûler au complet et on perdra de la puissance. C'est pourquoi on allumera la bougie avant que le piston se retrouve au point mort haut entre son temps de compression et d'explosion. Le mélange air-essence aura eu le temps de brûler un peu et la pression sera à son maximum lorsque ce sera le temps pour le piston de redescendre. On mesure le temps où la bougie s'allume en degré de rotation du vilebrequin. On dira ainsi que la plupart des moteurs ont une avance d'allumage de 20 degrés avant le point mort haut. On y va dans la langue de Shakespeare; « 20 degrees before top dead centre » ou en abrégé 20 deg. BTDC. C'est en général et c'est quelque-chose qui est normalement réglé par le constructeur. Par contre, des ajustements sont possibles et c'est là que votre mécanicien expérimenté entre en jeu. Ce serait trop long de vous expliquez ici tous les détails suffit de dire qu'en règle général si on avance trop l'allumage, disons 25 degrés BTDC, le mélange air-essence s'allumera alors que le piston est encore en train de remonter et on aura détonation (moteur scrappe) et une perte de puissance. Dans le cas contraire, disons 15 degrés BTDC, le mélange air-essence s'allumera quand le piston est en train de redescendre et la pression diminuera d'autant. Résultat, perte de puissance, essence non brûlés et émissions de polluants accrus. Bon maintenant, qu'on a compris ça oubliez tout ce que je viens de vous dire puisque les distributeurs ne sont plus utilisés depuis une bonne dizaine d'années. (Pas vrai essayez de vous en rappeler quand même un peu.)
La ou les bobines d'allumage (« ignition coil » en anglais ou simplement « coil »).
Au début je vous disais que les bougies nécessitent un voltage de 10 000 à 20 000 volts pour bien fonctionner. Évidemment, la batterie fournit seulement 12 volts, on doit donc trouver un moyen de faire augmenter le voltage. C'est le rôle de la bobine d'allumage. Elle fonctionne un peu comme un transformateur électrique accroché à un poteau de téléphone. On a des bobinages de fil de cuivre enroulés autour d'un fil qui part de la batterie. Ces bobinages, par induction électromagnétique, font augmenter le voltage qui est ensuite envoyé vers le distributeur. Et voilà on est passé de 12 à 10 000 volts. En réalité c'est un peu plus compliqué, mais c'est pas un cours d'électricien que je vous fais. Ce que vous devez savoir c'est que si jamais la bobine n'augmente pas le voltage suffisamment, les bougies n'allumeront pas et le moteur ne fonctionnera pas.
En conclusion je vous présent le petit schéma suivant.
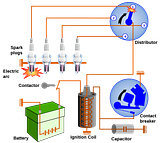
On a la batterie en vert qui fournit le courant à la bobine en gris foncé. Cette dernière augmente le voltage et envoi le courant dans le distributeur, les deux cercles en bleu. Ce dernier s'assure que chaque bougie, les quatre « bâtons » blancs, s'allument au moment désiré. Et voilà, le système d'allumage décrit en une seule image. Le petit truc écrit « capacitor » en anglais, est un accumulateur, ils s'assurent que toutes les interférences électriques qui pourrait être créés n'affectent pas les autres systèmes électriques de votre voiture. En clair, il est là pour ne pas que vous entendiez le distributeur au lieu de CHOI Radio X.
C'est tout pour ce soir, apprenez ça par cœur et je vous reviens avec la version électronique de tout ce bazar. Oh!, j'oubliais. Si vous avez des questions, gênez-vous pas pour vous servir de l'option « commentaires » du blog.
S'abonner à :
Messages (Atom)