Alors on continue aujourd’hui mes capsules mécaniques en terminant ma série d’article sur la suralimentation. Cela fait un petit bout de temps que je n’ai rien écris dans cette série, mon dernier billet remontant au mois de décembre 2010. Je vous dirige donc vers les articles précédents, la première partie et la deuxième partie. Dans cette troisième et dernière partie, je vous présente les systèmes de turbo-compresseur.
Comme les compresseurs volumétriques, les turbo-compresseurs ne servent qu’à faire entrer plus d’air dans le moteur. La manière d’y arriver est fort simple on augmente la pression dans la tubulure d’admission, faisant ainsi grimper la densité de l’air qui pénètre dans le moteur. Je ne reviendrai pas sur les spécificités d’une telle action, elles ont déjà été bien expliquées auparavant. La seule différence avec un compresseur volumétrique est que ce dernier est entraîné par la force moteur même tandis que le turbo-compresseur utilise la pression des gaz d’échappement, autrement perdus, pour compresser l’air d’admission. Les mêmes principes fondamentaux s’appliquent ici. Je vais donc plus me concentrer sur la partie mécanique du turbo-compresseur, qui est en fait, ce qui le différencie vraiment des compresseurs volumétriques. On commence à l’instant, avec la turbine
Turbine («turbine» ou «inducer» en anglais).
La turbine est très semblable au compresseur dans sa construction, sauf qu’elle fonctionne en «envers» . C’est-à-dire, qu’au lieu de compresser le gaz, elle recueille celui-ci pour le transformer en travail mécanique. Le gaz en question est celui des échappements que tout moteur à explosion produit de façon considérable. De plus, grâce au mouvement du piston et à l’ouverture des soupapes, ces gaz d’échappement ont une vélocité plutôt grande et donc une pression plutôt haute elle aussi. C’est cette pression et cette vélocité que la turbine récupèrera.
Normalement, la turbine est boulonnée à la sortie du collecteur d’échappement et une fois les gaz ayant été capté par cette dernière, ils sont dirigés directement dans la ligne d’échappement qui est boulonné sur le boîtier de la turbine. Par contre, ces dernières années pour des raisons d’efficacité et de coût, les turbines ont été intégrées directement au collecteur d’admission. Je vous en expliquerai les raisons plus bas.
Le principe de fonctionnement de la turbine est assez simple. Une série d’ailettes sont orientée et courbée de façon à transformer la vitesse et la pression du flux de gaz d’échappement en travail. Ce travail est rotatif et c’est lui qui fera tourner le compresseur. Le travail de la turbine est transmis par un arbre d’entraînement. Ce dernier doit évidemment, être lubrifié et soutenue. La plupart du temps ce sont des roulements en cuivre («bearings» en anglais) lubrifié par l’huile moteur, mais de plus en plus on utilise des roulements à bille ou à aiguille («ball bearings» en anglais) . De plus, due au positionnement du turbo-compresseur, il doit être refroidi, puisqu’il travail directement dans les gaz d’échappements qui peuvent atteindre des températures assez élevées. Plusieurs techniques sont utilisés. Les plus courantes, étant un refroidisseur d’huile qui refroidis à la façon d’un radiateur, toute l’huile moteur. Une petite conduite se rend alors dans le boîtier de l’arbre d’entraînement pour y prélever l’huile à refroidir et retourner celle qui l’est déjà. On peut aussi utiliser la même technique, mais cette fois avec le liquide de refroidissement intégral du moteur et son radiateur. Finalement, dans les systèmes haute-performance, on utilise généralement les deux, soit l’huile moteur et le liquide refroidissement. Bien évidemment, le radiateur de la voiture doit être conçu en conséquence, puisque le système de turbo-compresseur rajoute un autre système à refroidir. Les ingénieurs d’usine calculeront ces contraintes lors de la conception, mais les «tuners» ne le feront peut-être pas ce qui peut causer des dégâts catastrophiques, tant à la turbine qu’au moteur.
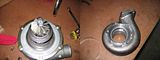
(On voit bien ici la turbine dans son boîtier, en fait une moitié du boîtier a été démontée pour rendre la turbine accessible.)
Compresseur («compressor» ou «impeller» ou «exducer» en anglais) .
Une fois l’énergie et le travail potentiel des gaz d’échappements récupérés par la turbine, ces derniers sont transmis au compresseur par l’arbre d’entraînement. Le compresseur est tout simplement le contraire de la turbine. Il sert à transformer le travail rotatif et l’impartir au flot d’air qui ira dans la tubulure d’admission. Le but ici étant de faire augmenter la pression. Encore une fois, une série d’ailettes à l’orientation et la courbure pré-définis se chargeront de ce travail. La forme et la position des ailettes est ce qui déterminera la pression ou plus précisément la surpression que le système de turbo-compresseur pourra fournir. Contrairement, à la turbine, normalement le compresseur ne demande pas de système de refroidissement. C’est la partie «froide» du système. Par contre, il ne faut pas oublier que tout gaz qui est compressé augmente en température. Cette température doit être évidemment contrôlée. C’est le rôle de l’échangeur d’air ou «intercooler», je vous en parle plus bas.
Le compresseur est lié mécaniquement à la turbine et vice-versa. Il faut bien comprendre ici que des conditions ou problèmes affectant l’un vont affecter l’autre. Par exemple, il n’y a pas vraiment de limite physique à la révolution à laquelle la turbine peut tourner. Tout dépendra de la pression et de la vitesse des gaz d’échappements. Par contre, le compresseur ne peut compresser l’air sans limite. La forme de ses ailettes fera qu’une fois une certaine révolution atteinte elles ne seront plus efficaces. C’est ce que l’on appelle la cavitation, à ce moment, les ailettes peuvent être grandement endommagées. De plus, le moteur comme tel a une limite mécanique à la quantité de surpression qu’il peut absorber. C’est un peu une roue sans fin. Plus la pression augmente dans le moteur, plus la pression des gaz d’échappements sera grande. Plus la pression est grande, plus la turbine tournera rapidement et plus celle-ci tourne vite plus le compresseur fournira de surpression. Il faut donc trouver un moyen de contrôler toute cette pression, pour ne pas faire exploser notre moteur. Je vous en parle à l’instant, mais il faut garder à l’esprit que ce n’est pas un problème auxquelles les moteurs à compresseur volumétrique sont sujets ou du moins, la plupart du temps.
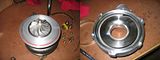
(Ici on voit bien le compresseur en tant que tel. Il est facile de comprendre la similitude avec la turbine.)
Soupape d’échappement et contrôleur de surpression («wastegate» et «boost controller» en anglais) .
Comment peut-on contrôler la vitesse à laquelle notre turbine tourne? Pour répondre à cette question je vous en pose une autre. Comment fait-t-on pour contrôler la pression dans la turbine? Je réponds à la deuxième et vous comprendrez tout de suite. Comme je vous le disais plus haut c’est la pression des gaz d’échappements qui fera tourner la turbine plus ou moins vite. Si on pouvait donc contrôler cette pression on pourrait contrôler la vitesse de la turbine. Évidemment, pas question de systèmes complexes de soupape ou de clapet dans le moteur ou même la culasse. Par contre, au niveau du boîtier de la turbine il y a quelque-chose à faire. On perce alors le dit boîtier et ferme l’orifice ainsi créé par une soupape. En actionnant la soupape une partie de la pression des gaz d’échappement sera alors détourner ailleurs que dans la turbine, la vitesse de rotation de celle-ci en sera alors d’autant réduite. C’est le rôle de la soupape d’échappement ou «wastegate» en anglais. Le diamètre du trou est alors étudié soigneusement pour ne pas ni enlever trop de pression ni en laisser trop à l’intérieur de la turbine. La forme du trou peut aussi être étudiée pour plus d’efficacité. Les gaz d’échappements s’échappant de la turbine ont longtemps été laissés à l’air libre, d’où le mauvais rendement d’émissions polluantes des moteurs turbos. Aujourd’hui, dans la plupart des cas, la soupape d’échappement de la turbine renvoie les gaz dans la ligne d’échappement de la voiture. Par contre, certains moteurs de courses ou des moteurs modifiés façon maison (les fameux «tuner»), n’hésite pas à relâcher le tout dans l’atmosphère. Passons.
Mais comment est-ce qu’on contrôle cette fameuse «wastegate» ? Eh! bien on a besoin d’un contrôleur de surpression ou «boost controller» en anglais. Il y a vraiment une panoplie énorme de façon de faire, mais dans la plupart des cas il s’agit d’un dispositif électronique ou mécanique qui va mesurer le degré de surpression dans la tubulure d’admission. Une fois une certaine mesure atteinte, il commande à la soupape d’échappement son ouverture et on contrôle ainsi sa vitesse de rotation. Le contrôleur de surpression est en fait une autre soupape qui bloque l’aspiration créé par un moteur en fonction, le fameux «vacuum» . La soupape s’ouvre alors et le «vacuum» aspire la soupape d’échappement de la turbine laissant s’échappé les gaz en trop. Le contrôleur de surpression peut aussi être ajustable, acceptant une surpression plus ou moins grande. Ce n’est pas vraiment commun dans les modèles de production, mais les voitures modifiées recourent souvent à ce genre d’artifice pour plus de puissance.
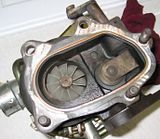
(On voit ici la soupape d'échappement à droite de la turbine.)
Soupape de décharge («blow-off valve» en anglais ou abrégé BOV).
Ce petit dispositif n’est pas obligatoire, mais très recommandé si on installe un système de turbo-compresseurs sur un moteur qui n’en était pas munis au départ. La soupape de décharge règle un problème commun à tous les moteurs turbo-compressés et même certains moteurs utilisant un compresseur volumétrique. Quoique ce soit beaucoup moins courant dans ce dernier cas. Le problème est l’inertie. Lorsqu’on déplace une grande quantité d’air elle accumule de l’énergie. Cette énergie est en partie ce qui sert à produire plus de puissance dans notre moteur. Par contre, le conducteur moyen n’utilisera pas son moteur à 100 %, 100 % du temps. En fait, dans un moteur moderne, quand on relâche l’accélérateur complètement, il n’y a aucune puissance de produite puisque aucune essence n’est injectée. Néanmoins, des gaz d’échappement et de l’air seront tout de même expulsé, dans le premier cas et admis dans le deuxième. Ce qui fait que notre système de turbo-compresseurs continuera à fonctionner et à produire une surpression. Alors qu’est-ce qui arrive à notre compresseur si on ferme le papillon des gaz. Sa surpression n’a plus aucun endroit où s’échappé. Soit la conduite d’admission saute ou le compresseur se met à tourner dans le sens contraire puisque l’air qu’il poussait n’a plus d’échappatoire. Ceci est très dommageable pour le compresseur et pour la turbine puisque rappelons-nous cette dernière reçoit toujours des gaz d’échappements. Il faut donc trouver un moyen pour laisser s’échapper cette surpression quand on ferme le papillon des gaz.
La solution est plutôt simple. On a une autre soupape qui est boulonné sur la tubulure d’admission. C’est la fameuse «blow-off valve» ou soupape de décharge en français. Cette dernière est plutôt simple. La soupape comme tel est montée dans un boîtier avec un ressort calibré derrière elle. Le ressort est calibré pour soutenir une certaine pression. Quand la pression est trop grande il se compresse laissant ainsi sortir le surplus d’air par la soupape qui est maintenant ouverte. Cela permet ainsi de ne pas endommager le système de turbo-compresseur. Normalement ce système s’il est installé à l’usine n’émet aucun bruit puisque souvent le surplus de pression est retourné dans la tubulure d’admission d’une manière ou d’une autre dépendant de ce que les ingénieurs croient être le plus efficace. Par contre, dans les systèmes turbo dit «aftermarket» ou de remplacement souvent la soupape de décharge libère la pression directement à l’air libre. C’est ce qui produit le fameux «pshhht» caractéristique des moteurs modifiés avec un turbo-compresseur. De plus, certaines soupapes de décharge sont désigné pour produire un bruit distinctif. Cela n’ajoute rien aux performances du moteur, mais c’est un bruit que certain trouve très agréable et cela permet à tout le monde de savoir que votre moteur est turbo-compressé.
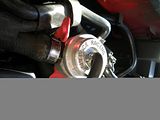
(Une photo en rapproché d'une soupape de décharge à recirculation. C'est-à-dire que les gaz en surpression sont renvoyé dans la tubulure d'admission après le papillon des gaz.)
Échangeur d’air ( «intercooler» en anglais).
Je vous avais déjà expliqué le fonctionnement et les avantages d’un échangeur d’air dans mon article sur les compresseurs volumétriques. Les mêmes avantages sont présent dans un système de turbo-compresseur. En fait, dans un tel système, l’emploi d’un échangeur d’air est presque obligatoire. Premièrement, la quantité de surpression est souvent beaucoup plus importante dans un turbo-compresseur, alors l’air est beaucoup plus chaud que dans un compresseur volumétrique. Il faut donc absolument la refroidir pour ne pas avoir de perte de puissance trop importante. De plus, le fonctionnement intrinsèque d’un turbo-compresseur, en utilisant les gaz d’échappement, fait qu’il y a nécessairement un échange de chaleur entre les pièces mécaniques du système et l’air ambiant qu’il «pompe» dans le moteur. C’est pourquoi la très grande majorité des systèmes de turbo-compresseur en sont équipés.
«Turbo-lag» .
Désolé, je n’ai pas traduction en français pour ce phénomène, je vous explique plutôt de quoi il s’agit. On a vu plus haut que la turbine se servait des gaz d’échappement pour faire son travail. C’est la vitesse et la pression de ces derniers qui détermineront la vitesse à laquelle elle tournera et par le fait même, la vitesse du compresseur et donc la surpression admise dans la tubulure d’admission. Bien évidemment, la pression des gaz d’échappement est proportionnelle au régime moteur. Plus le moteur tourne vite plus la pression des gaz sera élevée, mais le contraire est vrai aussi. Dans un système de turbo-compresseur on essais toujours d’optimiser la réponse de la turbine au régime-moteur, mais tout étant affaire de compromis on ne peut pas avoir toujours la même surpression partout dans le compte-tours. Ce manque de surpression et donc de puissance est ce que l’on appelle le «turbo-lag» . La turbine doit avoir un minimum de pression pour pouvoir faire son travail sinon, elle ne produira pas plus de puissance et peut même devenir une entrave au bon fonctionnement du moteur en bloquant la sortie des gaz d’échappement.
Au volant, on sentira le «turbo-lag» comme un manque de puissance à plus ou moin bas régime. Une fois que la turbine a assez de gaz pour travailler, la puissance augmentera radicalement et de beaucoup. On aura donc un bon coup de sabot dans les reins. Le problème que cela peut poser c’est que c’est le conducteur qui doit anticiper cette arrivée de puissance et elle se fera peu importe les conditions routières ou d’utilisation. Un cas célèbre est la première génération de 911 Turbo. Déjà la voiture à l’époque était délicate à conduire, mais en plus en lui rajoutant un turbo, on lui donnait un surplus de puissance qui n’arrivait pas toujours au bon moment. Le «turbo-lag» fut probablement responsable de plusieurs sorties de route inopportune.
Il y a plusieurs façon de régler ce problème. La plus facile, mais aussi la plus coûteuse en temps et en énergie est de simplement calibré la turbine en fonction du moteur sur lequel elle sera montée ainsi que la puissance que l’on désire avoir. C’est quelque-chose qui est faisable, mais surtout par les ingénieurs d’usine qui ont toutes les données à leur disposition pour faire ce travail. Le fait d’avoir un roulement dans l’arbre d’entraînement avec le moins de friction possible est aussi une autre façon d’amenuiser le «turbo-lag» . Il y a d’autres façons plus radicale de régler le problème et c’est ce que je me propose de vous décrire à l’instant.
Bi-Turbo.
Les systèmes bi-turbo utilisent deux turbines ou plus. Par exemple, la Bugatti Veyron 16.4 utilise 4 turbos pour son moteur 16 cylindres. La raison en est fort simple et utilise une loi de physique fondamentale. À cause de l’inertie, plus la turbine est grosse plus elle sera difficile à déplacer. Par contre, à part quelques exceptions, plus la turbine est grosse plus elle pourra accomplir de travail. Si vous avez compris ce que je disais plus haut, plus la turbine est grosse plus il y a aura de «turbo-lag» . Les systèmes bi-turbo essais de contourner le problème en utilisant deux plus petites turbines pour accomplir le travail d’une seule grosse. Le système est plus complexe et coûteux qu’un seul turbo-compresseur, mais cela reste un bon moyen d’éviter le «turbo-lag» . Il y a quelques contraintes. Idéalement, il faut qu’il s’agisse d’un moteur en V pour pouvoir mettre un turbo par banc de cylindres, mais BMW a réussi à monter un bi-turbo sur son 6 cylindres en ligne dans les 335i et autre 135i.
Turbo séquentiel.
Une autre solution et un peu semblable au système bi-turbo, est de montée une petite turbine en série avec une plus grosse turbine. Lorsque le régime moteur est bas, c’est la petite turbine qui fournit la puissance au compresseur. Quand le régime moteur est assez haut, un clapet dans le collecteur d’admission bouge et c’est maintenant la grosse turbine qui fait fonctionner le compresseur. On peut aussi avoir deux compresseurs, un gros et un petit chacun accouplé à sa turbine. Ou encore, la petite turbine peut servir à accélérer le flot de gaz d’échappement dans l’intrados de la grosse turbine. Bref, les configurations sont presque infinies. Deux véhicules notoires ayant utilisés cette technologie sont la Toyota Supra Turbo de 1996 et toutes les Nissan Skyline GT-R jusqu’à l’actuelle R35, qui elle utilise un système bi-turbo.
Twin-Scroll.
Encore un terme anglophone dont je n’ai pas la traduction française. Il s’agit en fait d’un collecteur d’admission séparant le flux de gaz d’échappement pour créer le moins d’interférence possible. C’est un peu compliqué alors ne vous prenez pas la tête si vous ne comprenez pas. Ce qui arrive, c’est qu’étant donné que les gaz d’échappement sont en fait contrôlés par l’ouverture des soupapes d’échappement et que celles-ci ne sont pas ouverte continuellement, le flot de gaz d’échappement n’est pas continue, mais plutôt pulsé. Chaque impulsion de gaz voyage ainsi séparément dans le collecteur d’échappement et se rejoint plus bas dans la ligne d’échappement. Chaque impulsion peut par contre interférer avec les autres créant ainsi un flot inverse vers le moteur. C’est en partie ce qui créé la fameuse «backpressure» dans les systèmes d’échappement. Ces interférences font que le turbo ne recevra pas une quantité égale de gaz d’échappement dépendant du régime moteur et d’autres facteurs plus compliqués et qui sortent un peu de l’objectif de mon article. Ce que le collecteur d’échappement «Twin-Scroll» fait c’est qu’il sépare chaques cylindres du moteur et, d’après une chemin plus ou moins compliqué de la tuyauterie, s’organise pour que le turbo reçoivent le flot de gaz d’échappement le plus continue possible. De plus, certains collecteur «Twin-Scroll» peuvent carrément bloquer l’arrivée des gaz d’échappement de certains cylindres pour une meilleure efficacité du turbo. Comme je vous le disais, c’est plutôt compliqué, mais ce qu’il faut retenir c’est qu’un collecteur d’échappement «Twin-Scroll» sert à optimiser le flot des gaz d’échappement dans la turbine du turbo-compresseur.
Géométrie variable.
Les systèmes à géométrie variable existent depuis longtemps dans l’aviation, mais surtout dans les centrales hydroélectriques où ce type de dispositif est courant. Il s’agit de placer des vannes directrices dans la circonférence de la turbine. Ces vannes bougent et peuvent ainsi faire augmenter la pression ou la faire diminuer de façon relativement indépendante de la pression dans le collecteur d’échappement. En fait, il s’agira plutôt ici de la vélocité des gaz d’échappement ou si vous préférez de leur débit. Les vannes permettant de transformer ce débit en pression. Ces dernières sont contrôlées par l’ordinateur de bord. Le tout est très dispendieux et c’est pourquoi il est assez rare de retrouver ce type de turbine dans l’automobile. La Porsche 911 Turbo type 997, donc la dernière génération, utilise ce type de turbo-compresseur, mais on parle tout de même d’une voiture valant quelques 200 000$.
Injection d’essence dans le collecteur d’échappement (communément appelé «anti-lag» en anglais).
Une autre façon d’amoindrir le «turbo-lag», mais cette fois beaucoup plus radicale, est de réinjecter de l’essence dans le collecteur d’échappement. La température à cet endroit aidant, l’essence s’enflammera et les gaz ainsi chauffés prendront de l’expansion, augmentant d’autant la pression pour la turbine. Aucune voiture civile n’est équipée d’un tel système, puisque les émissions polluantes seraient énormes et la pollution sonore en prendrait pour son rhume. On retrouve normalement ce dispositif dans des voitures de courses, plus particulièrement les voitures courant dans le championnat du monde de rallye. D’ailleurs pour ceux qui suivent ce genre de compétition, vous serez habitués d’entendre les moteurs crépités à tout rompre et plus de chuintement et de sifflement, c’est tous les systèmes mentionnés plus hauts ainsi que le système «anti-lag» qui se font entendre. Pas sur que vous voudriez que la voiture de votre voisin couche-tard en soit équipée.
Conclusion.
Il y aurait bien d’autres sujets à aborder concernant la suralimentation, mais c’est un domaine plutôt complexe. Mes capsules mécaniques se veulent plus des articles d’introduction que des études en profondeur et il y aurait de quoi écrire plusieurs livres sur le sujet. C’est d’ailleurs le cas, si vous voulez plus de détails allez à votre bibliothèque de quartier ou allez faire un tour sur les librairies en ligne, il y a une tonne d’ouvrages sur le sujet. En attendant, j’espère que je n’ai pas été trop technique à votre goût, mais c’est plutôt difficile de ne pas l’être avec un tel sujet. À la prochaine leçon!
Aucun commentaire:
Publier un commentaire